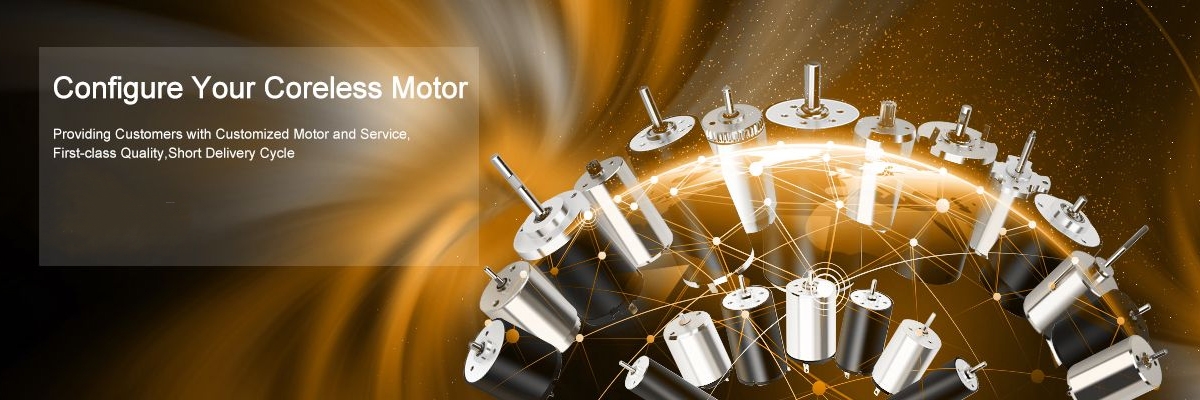
In the operation of low-noise DC geared motors, noise levels can be maintained below 45 decibels. These motors, comprising a driving motor (DC motor) and a reduction gearbox, significantly enhance the noise performance of traditional DC motors. To achieve noise reduction in DC motors, several technical strategies are employed. The construction encompasses a DC motor body with a rear cover, two oil bearings, brushes, a rotor, a stator, and a reduction gearbox. The oil bearings are integrated within the rear cover, and the brushes extend into the interior. This design minimizes noise generation and prevents excessive friction typical of standard bearings. Optimizing brush settings reduces friction with the commutator, thereby lowering operational noise. Strategies to mitigate motor noise include:
- Reducing wear between carbon brushes and the commutator: Emphasizing precision in the lathe processing of DC motors. The optimal approach involves refining technical parameters through experimentation.
- Noise issues often stem from rough carbon brush bodies and inadequate running-in. Prolonged operation can lead to commutator wear, overheating, and excessive noise. Recommended solutions include smoothing brush bodies to enhance lubrication, replacing the commutator, and regularly applying lubricating oil to reduce wear.
- To address noise generated by DC motor bearings, replacement is advised. Factors such as excessive compression, improper force application, overly tight fits, or unbalanced radial forces can cause bearing damage.
Sinbad Motor is dedicated to manufacturing motor equipment solutions that excel in performance, efficiency, and reliability. Our high-torque DC motors are vital in multiple high-end industries, including industrial production, medical equipment, automotive, aerospace, and precision devices. Our product range encompasses a variety of micro-drive systems, from precision brush motors to brushed DC motors and micro geared motors.
Writer: Ziana
Post time: Sep-04-2024