Brushless DC motor (BLDC) is a high-efficiency, low-noise, long-life motor that is widely used in various fields, such as industrial automation, power tools, electric vehicles, etc. Speed regulation is an important function of brushless DC motor control. Several common brushless DC motor speed regulation methods will be introduced below.
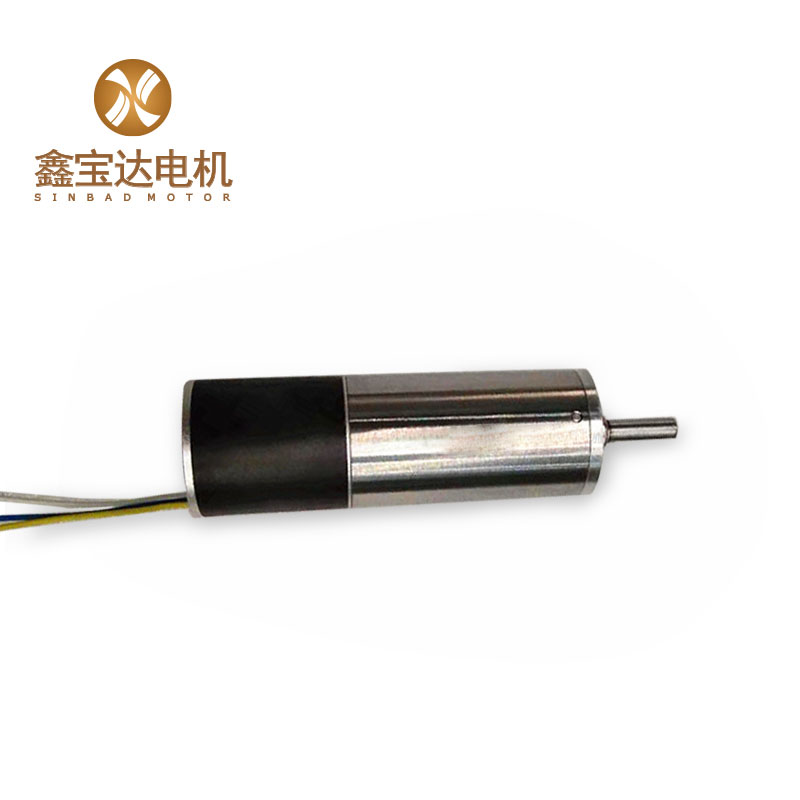
1. Voltage speed regulation
Voltage speed regulation is the simplest speed regulation method, which controls the speed of the motor by changing the voltage of the DC power supply. When the voltage increases, the motor’s speed will also increase; conversely, when the voltage decreases, the motor’s speed will also decrease. This method is simple and easy to implement, but for high-power motors, the effect of voltage speed regulation is not ideal, because the efficiency of the motor will decrease as the voltage increases.
2. PWM speed regulation
PWM (Pulse Width Modulation) speed regulation is a common method of motor speed regulation, which controls the speed of the motor by changing the duty cycle of the PWM signal. When the duty cycle of the PWM signal increases, the average voltage of the motor will also increase, thereby increasing the motor speed; conversely, when the duty cycle of the PWM signal decreases, the motor speed will also decrease. This method can achieve precise speed control and is suitable for brushless DC motors of various powers.
3. Sensor feedback speed regulation
Brushless DC motors are usually equipped with Hall sensors or encoders. Through the sensor’s feedback of the motor’s speed and position information, closed-loop speed control can be achieved. Closed-loop speed regulation can improve the speed stability and accuracy of the motor, and is suitable for occasions with high speed requirements, such as mechanical equipment and automation systems.
4. Current feedback speed regulation
Current feedback speed regulation is a speed regulation method based on motor current, which controls the motor speed by monitoring the motor current. When the load of the motor increases, the current will also increase. At this time, the stable speed of the motor can be maintained by increasing the voltage or adjusting the duty cycle of the PWM signal. This method is suitable for situations where the motor load changes greatly and can achieve better dynamic response performance.
5. Sensorless magnetic field positioning and speed regulation
Sensorless magnetic field positioning speed regulation is an advanced speed regulation technology that uses the electronic controller inside the motor to monitor and control the motor’s magnetic field in real time to achieve precise control of the motor speed. This method does not require external sensors, simplifies the structure of the motor, improves reliability and stability, and is suitable for situations where the volume and weight of the motor are high.
In practical applications, multiple speed regulation methods are usually combined to achieve more precise and stable motor control. In addition, the appropriate speed regulation scheme can be selected according to specific applications and requirements. The speed regulation technology of brushless DC motors is constantly developing and improving. In the future, more innovative speed regulation methods will appear to meet the needs of motor control in different fields.
Writer:Sharon
Post time: Apr-24-2024