Servo motors and stepper motors are two common motor types in the field of industrial automation. They are widely used in control systems, robots, CNC equipment, etc. Although they are both motors used to achieve precise control of motion, they have obvious differences in principles, characteristics, applications, etc. Below I will compare servo motors and stepper motors from many aspects to better understand the differences between them.
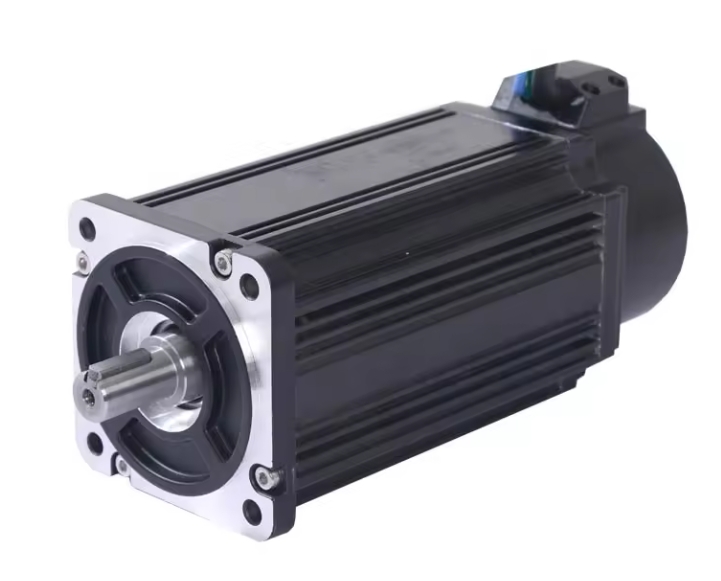
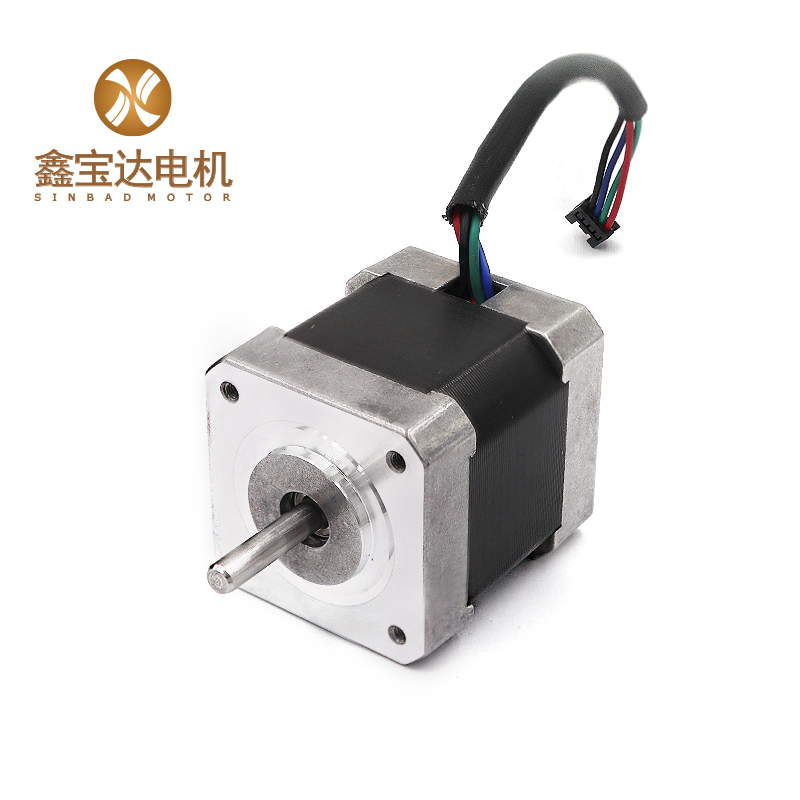
- Principle and working method:
A servo motor is a motor that can accurately control position, speed and torque according to instructions from the control system. It usually consists of motor, encoder, controller and driver. The controller receives the feedback signal from the encoder, compares it with the set target value and the actual feedback value, and then controls the rotation of the motor through the driver to achieve the expected motion state. Servo motors have high precision, high speed, high responsiveness and large output power, making them suitable for applications requiring precision control and high performance.
A stepper motor is a motor that converts electrical pulse signals into mechanical motion. It drives the rotation of the motor by controlling the magnitude and direction of the current, and rotates a fixed step angle each time it receives a pulse signal. Stepper motors have the characteristics of simple structure, low cost, low speed and high torque output and no need for feedback control. They are suitable for some low speed and low precision applications.
- Control method:
Servo motors usually adopt closed-loop control, that is, the actual status of the motor is continuously monitored through feedback devices such as encoders and compared with the target value set by the control system to achieve precise position, speed and torque control. This closed-loop control allows the servo motor to have higher accuracy and stability.
Stepper motors usually use open-loop control, that is, the rotation of the motor is controlled based on the input pulse signal, but the actual status of the motor is not monitored through feedback. This type of open-loop control is relatively simple, but cumulative errors may occur in some applications that require precise control.
- Performance characteristics:
Servo motors have high precision, high speed, high responsiveness and large output power, making them suitable for applications requiring precision control and high performance. It can achieve precise position control, speed control and torque control, and is suitable for occasions requiring high-precision motion.
Stepper motors have the characteristics of simple structure, low cost, low speed and high torque output and no need for feedback control. They are suitable for some low speed and low precision applications. It is usually used in applications that require large torque and relatively low precision, such as printers, CNC machine tools, etc.
- Application areas:
Servo motors are widely used in situations that require high precision, high speed, and high performance, such as CNC machine tools, robots, printing equipment, packaging equipment, etc. It plays an important role in automation systems that require precision control and high performance.
Stepper motors are usually used in some low-speed, low-precision, cost-sensitive applications, such as printers, textile machinery, medical equipment, etc. Due to its simple structure and low cost, it has certain advantages in some applications with higher cost requirements.
To sum up, there are obvious differences between servo motors and stepper motors in terms of principles, characteristics, and applications. In practical applications, it is necessary to select the appropriate motor type according to specific needs and conditions to achieve the best control effect.
Writer:Sharon
Post time: Apr-17-2024