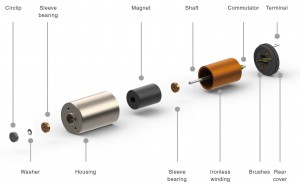
Compared to small motors, the bearing system of large motors is more complex. It doesn't make much sense to discuss motor bearings in isolation; instead, the discussion should encompass related components such as shafts, bearing housings, end covers, and inner and outer bearing covers. The compatibility with these associated parts is merely a mechanical fit, but Ms. Can believes that it should also take into account external factors such as the operating conditions of the motor.
In the actual operation and use of motors, the most common issue is the noise from the bearings. This problem may be related to the quality of the bearings themselves on one hand, and on the other hand, it may be related to the selection of bearings. Most of the issues stem from inappropriate or unreasonable practices in the manufacturing process that lead to bearing problems.
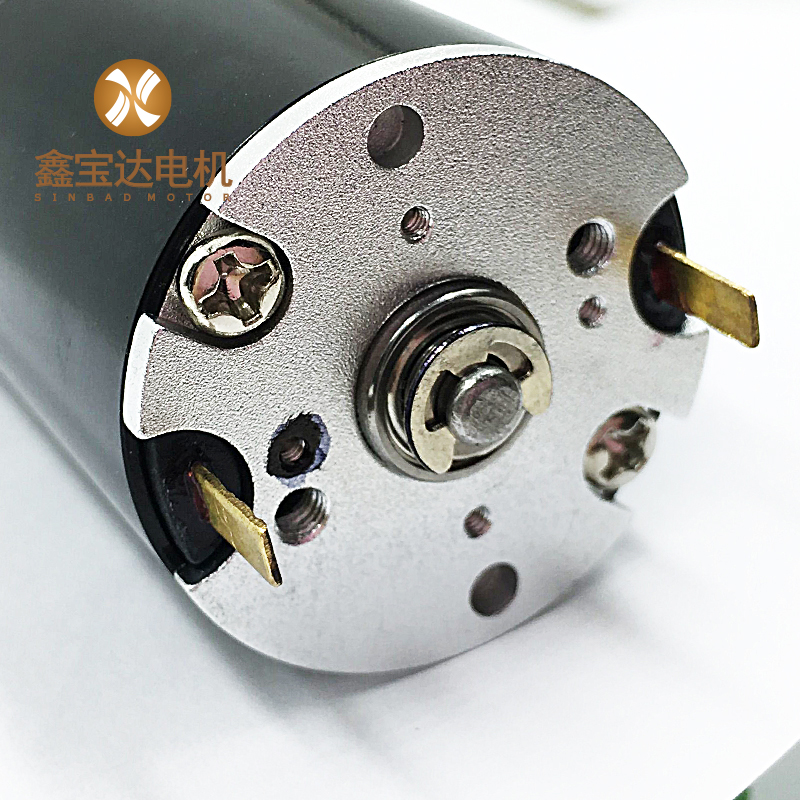
We know that noise originates from vibration. To address the noise issue of bearings, the primary issue to solve is vibration. Compared to small motors and general motors, large-scale motors, high-voltage motors, and variable frequency speed control motors also face the issue of shaft current. To solve this issue, one can use insulated bearings, but the procurement cost of these bearings is relatively high, and some insulated bearings are not yet widely available. Another approach is to use grounding carbon brushes, but this method is more troublesome to maintain. In light of this situation, many motor manufacturers are looking for solutions on the bearing housing and have invented insulated bearing housings. However, these insulated bearing housings are more complex to manufacture. The basic principle is to divide the bearing housing into two parts and insulate the bearing chamber part, thus completely cutting off the circuit caused by shaft voltage and shaft current, which is a one-time solution. The following figure is a partial view of an insulated bearing housing.
This type of insulated bearing housing can be divided into an inner sleeve and an outer sleeve, with an insulating filler between the inner and outer sleeves. The thickness of the insulating filler layer is 2-4mm. This insulated bearing housing, through the insulating filler layer, separates the inner sleeve and the outer sleeve, serving to block shaft current, thereby protecting the bearings and extending their service life.
Some coreless motor manufacturers also use insulating boards to achieve this effect, but the insulating performance of the insulating boards will decrease when they become damp. Additionally, there may be air gaps between the two column surfaces due to uneven thickness of the insulating board or the column surfaces not meeting the required roundness, which may have some impact on the performance of the bearing housing. It is recommended to take necessary remedial measures.
Writer:Ziana
Post time: Sep-24-2024