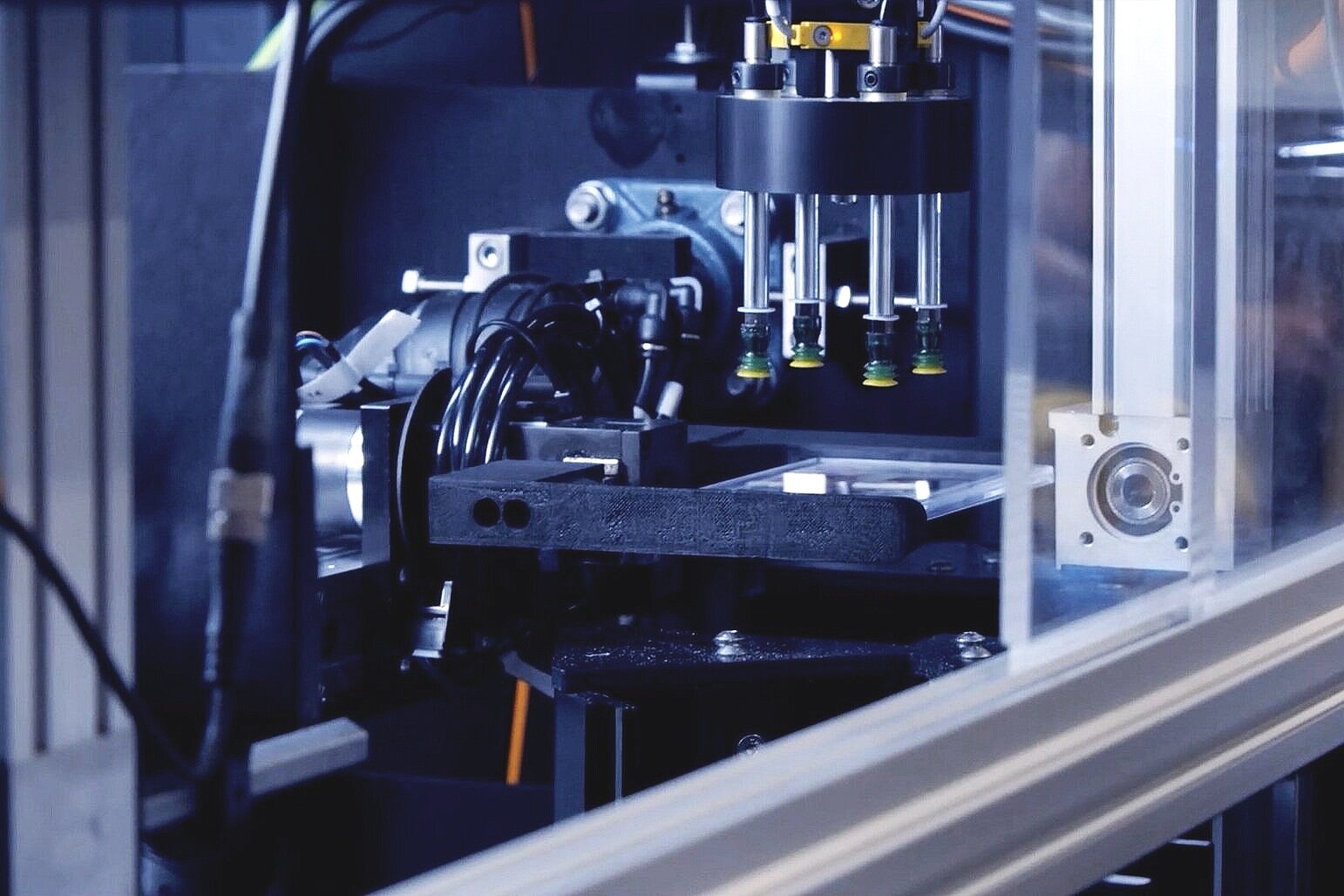
Motors are the heartbeat of industrial automation, pivotal in powering the machinery that drives manufacturing processes. Their ability to convert electrical energy into mechanical motion meets the need for precise and controlled movements in many robotic systems.
Types of Industrial Motors
Motors are classified into different types:
- DC motors, powered by direct current, are most suitable for applications demanding continuous and controlled motion. Their simple design and ease of speed control make them ideal for a wide range of industrial automation tasks.
- AC motors, powered by alternating current, are known for their efficiency and reliability. They are often preferred for high-power and constant-speed applications, such as pumps, compressors, and conveyors.
- Servo motors, are closed-loop systems that use positional feedback to maintain a desired position or speed in real time. They are best suited for high-precision tasks, like CNC machining, robotics, and automated inspection systems.
- Stepper motors, move in discrete steps without the need for positional feedback, allowing for precise control over position and speed. They are ideal for applications requiring accurate positioning and designs that are simpler than servo motors, such as 3D printing and medical devices.
The Growth of Brushless Motors in Industrial Applications
The increased use of brushless motors is driven by technological advancements and growing demand for efficient and reliable systems. As the name implies, brushless motors replace the mechanically driven functions of brushed motors with an electronic drive. The electronic controller creates a variable current that powers a magnetic field to create the motor’s spinning motion.
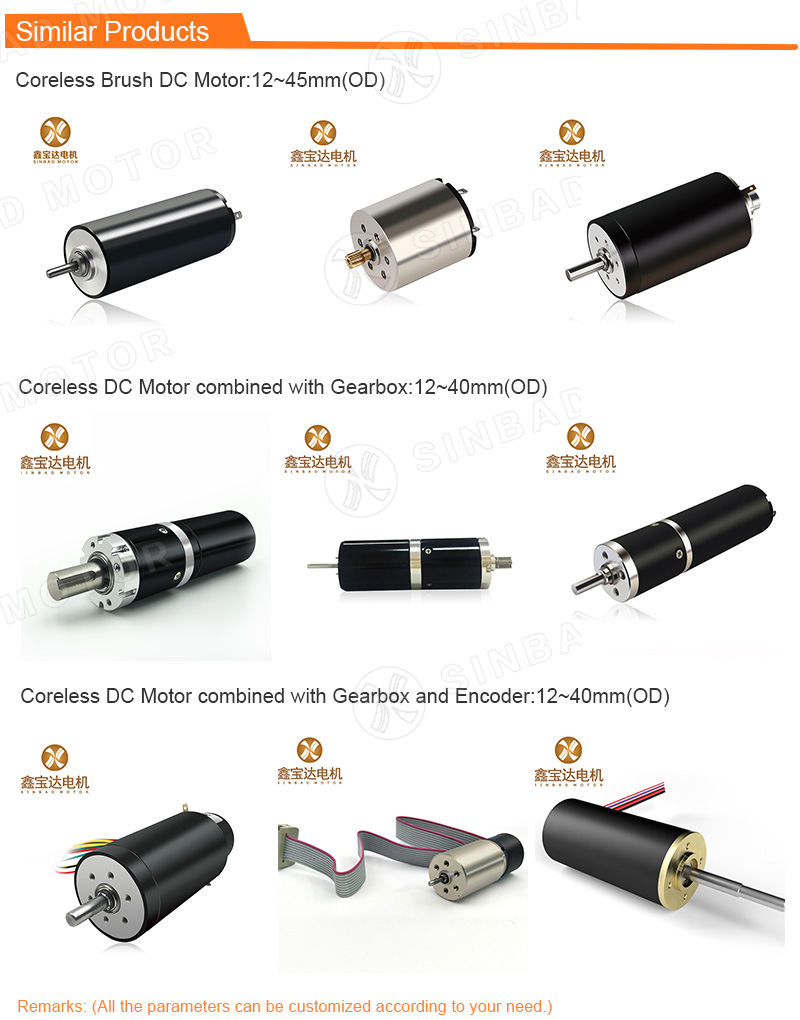
Considerations for Choosing the Right Motor
Businesses rely on motors to run their operations reliably and effectively regardless of the application. Consider these four factors when selecting your next industrial motor:
1. Performance Requirements
Understanding the specific performance requirements of a given application determines which features will take priority when you are selecting a motor.
High-speed operations require motors with fast response times, precision tasks need high accuracy, and heavy-duty applications demand high torque.Successfully addressing such requirements plays a major role in meeting business objectives around productivity, energy efficiency, scalability, and maintenance costs. High-efficiency motors, for example, can reduce energy consumption, while reliable and precise motors can enhance product quality and reduce downtime.
2. Environmental Conditions
Factors such as temperature, humidity, and exposure to dust or chemicals will also determine your motor selection. For applications in harsh environments, like foundries or chemical plants, motors with robust enclosures and resistance to environmental stressors are essential.
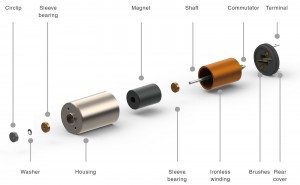
3. Power Supply and Voltage
Matching the motor’s power supply requirements with the available voltage is critical. An inadequate power supply can lead to underperformance or damage, while an oversized supply can reduce the motor’s life expectancy.
The key power supply considerations are:
- Voltage and current compatibility: Motors operate within specific voltage and current ranges. A mismatched voltage can lead to inefficiency, overheating, or failure.
- Power rating and capacity: Motor power ratings indicate their ability to convert electrical power. Compatibility with the power supply prevents overload or underutilization.
- Frequency (AC motors): AC motors operate at specific frequencies. Matching the power supply frequency is crucial for efficient synchronous operation.
- Start-up and operating conditions: Motor start-up conditions are influenced by the power supply and selecting units with the right characteristics prevents issues during initial demands.
- Control system compatibility: To work optimally in applications that require high precision, such as motion control and 3D printing, motors must be compatible with the requirements of their power supply control systems.
- Efficiency and energy consumption: Matching the motor to the power supply is essential for promoting energy efficiency, which is central to minimizing operational costs and ensuring sustainability.
- Safety: Understanding power supply requirements is vital for implementing adequate safety measures. Higher DC voltage motors may require additional precautions compared to those running on lower voltages.
The best motor is the one that meets the application’s requirements. From the simplicity of DC motors to the precision of servo motors, each type has its strengths. Careful consideration of factors specific to your business is essential for success.
Sinbad Motor is at the forefront of motor technology, dedicated to pushing the boundaries of what is possible in robotics and automation. Our commitment to innovation and excellence ensures that our coreless motors are at the heart of this technological revolution.
Writer
Ziana
Post time: Jul-10-2024