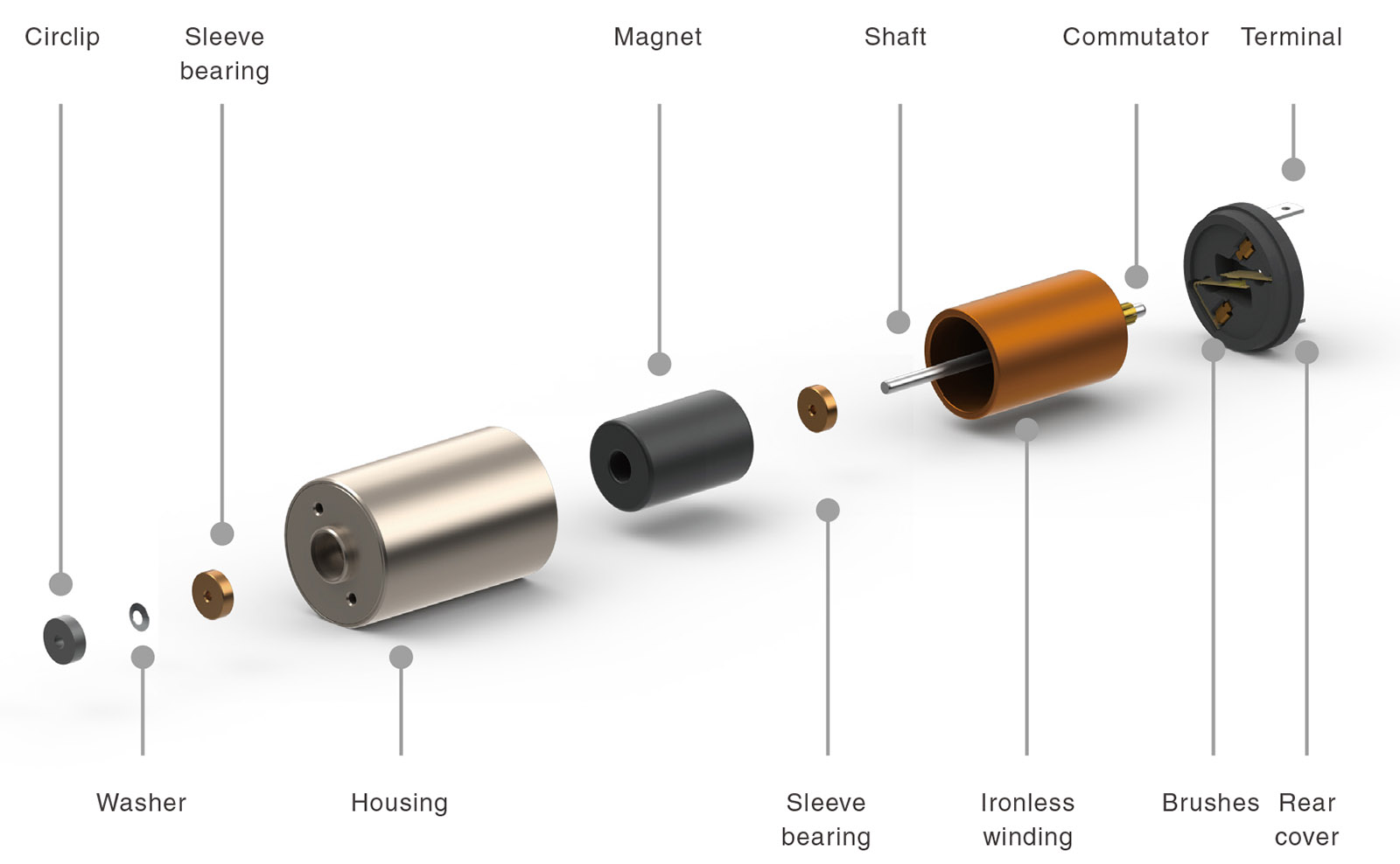
If you’ve got a gear motor that’s been hanging out in a damp spot for too long and then you fire it up, you might find its insulation resistance has taken a nosedive, maybe even to zero. Not good! You’ll want to dry it out to get those resistance and absorption levels back where they should be. Starting it up all damp could spell trouble, like coil insulation going belly-up and maybe even an accident. Let’s check out the right way to dry out those motors when they’ve been hanging with moisture.
Electric Welder Drying Method
To dry a gear motor with an electric welder, first connect the winding terminals in series and ground the motor’s case. This allows the windings to heat up and dry. Hook up an ammeter to check if the current reaches the motor’s rated value. This method, using an AC welder, saves time as you don’t need to disassemble the motor. The motor heats up through its own resistance, ensuring even heating of the coils for effective drying. But be cautious, as this method isn’t suitable for all gear motors and prolonged use can overheat the welder due to excessive current.
So, wiring up a DC welding machine is a lot like doing an AC one, but don’t forget the DC ammeter. It’s a breeze to dry out a soggy gear motor with a DC welder, especially if it’s a big gun or a high-voltage one that needs a good long dry. The DC machine can take the heat without getting fried. Just a tip: when you’re doing this, make sure all your connections are snug as a bug in a rug. Use the right wires for the job, and make sure they’re chunky enough to handle the current your welder pumps out.
External Heat Source Drying Technique
For gear motors affected by moisture, the initial step involves disassembly and thorough inspection. Subsequently, a high-wattage incandescent bulb can be placed within the gear motor for the drying process, or the motor can be positioned in a dedicated drying room. This technique is straightforward, secure, and dependable, yet it is only applicable to smaller gear motors that are readily disassembled and inspected. It is crucial to ensure that the bulbs or heating elements are not positioned too near to the coils to avoid coil overheating. Additionally, the use of canvas or similar materials to cover the gear motor’s casing can aid in heat retention.
Sinbad is committed to crafting motor equipment solutions that are outstanding in performance, efficiency, and reliability. Our high-torque DC motors are crucial in several high-end industries, such as industrial production, medical devices, the automotive industry, aerospace, and precision equipment. Our product range includes a variety of micro drive systems, from precision brushed motors to brushed DC motors and micro gear motors.
Writer: Ziana
Post time: Sep-19-2024